为何要将PLM 扩展到制造部门?
更多情况下,PLM 最初是作为许多公司的 CAD/设计数据库,后来发展为设计数据交换平台。大多数成功的公司正在将 PLM 不仅仅作为设计数据交换和访问控制平台;知识驱动的决策支持系统。这意味着PLM不仅需要管理产品生命周期各个阶段生成的大量信息,还需要捕获产品开发知识并将其反馈到产品生命周期。例如,产品新版本的需求和设计还需要由从先前版本的生命周期(从开始到设计到制造和服务)中捕获的知识元素来驱动。
当 PLM 仅仅停留在设计工程领域时,它只能从由互不相连的筒仓系统管理的下游阶段交换信息和获取知识。这导致工程师在数据采集任务上花费大量时间。行业研究表明,信息工作者花费30-40%的时间只用于信息收集和分析,从而将时间浪费在搜索不存在的信息、未能找到现有信息、验证信息或重新创建无法找到的信息上。
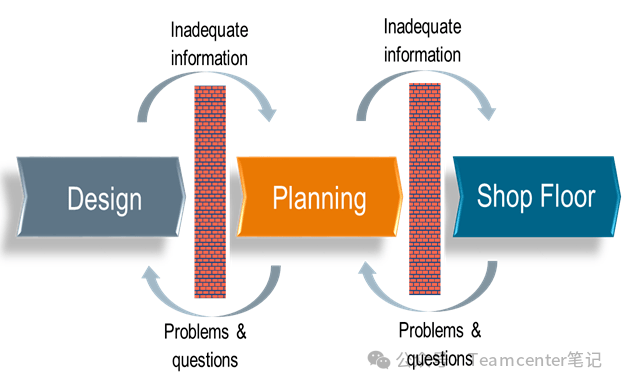
当产品不符合工程定义时,质量逃逸是此类断开系统的另一个挑战。在车间发现的不合格品的审查和处理成本很高,当产品已经投入使用时,情况会更加严重。协调变革也极具挑战性,尤其是其下游传播,导致生产力严重损失。变更处理缓慢以及质量问题导致新产品推出的延迟,影响了公司的整体竞争能力。
将 PLM 转变为真正的知识驱动决策支持系统的第一步是将其扩展到 CAD/CAM/CNC 流程链,从而将其带到车间。这样的解决方案有助于建立从工程到车间的运营管理和制造执行系统 (MES) 的连续循环。这种连续循环系统提供了更多捕获商业智能的方法,然后根据先前的模式提出解决方案。与当今许多公司所拥有的分散的解决方案相比,捕获信息并使用分析来综合有价值的知识元素要容易得多。它也是根据工业 4.0 愿景建立数字孪生的基本要素
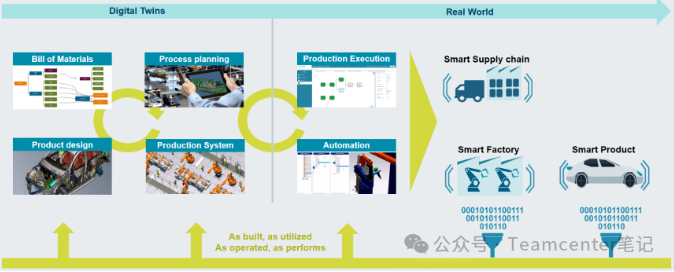
将 PLM 扩展到制造业的其他主要优势包括
缩短上市时间:增强产品和制造工程之间的协作;增强的可追溯性和更快的变更管理。
增强灵活性:制造计划涵盖产品的可变性/复杂性;用于优化决策的“假设”场景。
提高质量:PLM 中集成的制造仿真和验证;最新的 3D 工作说明交付到车间。
提高效率:基于利用率数据闭环反馈的持续流程优化;常用方法/工具的重用。
获取 达索PLM免费试用、体验