基于达索系统3DE平台实现企业数字化转型的场景应用
数字化转型的浪潮下,制造企业在不断变化的市场趋势中,面临越来越多的挑战,企业主在应对变化的同时,思考如何借助数字化转型契机,在竞争中赢得先机。本文从基于达索系统3DExperience数字化平台的落地场景,展现端到端的全流程管控。
1, 市场趋势与挑战并存
随着体验经济时代的到来,市场逐渐从增量时期转向存量时期。传统制造企业在产品品质、价格上的激烈竞争,逐渐转化为以客户需求的体验为新的利润增长点。这种转化形成市场趋势包括更短的交付周期,更复杂或者更具有颠覆性的产品设计,更为严苛的质量控制,更个性化的客户需求和细腻的客户体验,甚至是更为多元化的商业模式。
制造业在市场竞争中想要差异化并立于不败之地,要从自身甚至整个供应链中去寻求如何面对业务挑战。
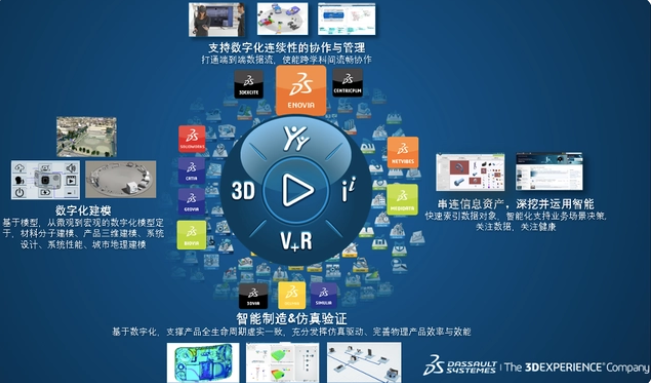
通过达索系统3DExperience数字化平台,可以实现协同效率提升,产品能力创新,研发制造全流程追溯,客户经营和商业模式创新。对于供应链的管理也是有迹可循,通过平台实现对于供应商的能力和要求的提升,转化压力,大大提升效率。
供应商将面对来自主机厂或者总装厂更高的要求,承担更多设计责任,提升人员的专业能力,同步更多创新想法,缩短交付周期,更精益的管控过程的成本和质量等。
2, 达索系统数字化企业业务场景
新一代数字化平台可以实现端到端的全流程管控,打通数字化营销到数字化研发,再到数字化制造。以数字化研发为例,在数字化平台是如何实现落地的场景:
2.1建设基于“需求跟踪矩阵” 的客户需求管理
企业在数字化营销阶段,需要通过数字化平台,将客户的需求快速进行转化,通过建立项目需求管理,将产品需求和设计需求通过数字化进行表达,构建BOM,在经过过程设计与开发,产品的验证,再到初期量产,订单满足验证。这个过程,通过BOM这个被各个业务领域频繁使用的交付物,管理整个产品的生命周期。
2.2 建设基于“大数据” 的可视化业务智能
通过新一代协同平台,集成企业内外多种数据源,将第三方系统,多层级Excel表格等数据文件,采用丰富直观的图表化界面,多层次、多角度、多形式地展现机构、流程、项目或任务执行过程的信息、状态或指标,便于领导快速决策。
2.3建设基于“主机厂上下文环境” 的主机厂数据管理
平台化的数据管理,解决了“信息孤岛”的问题,通过单一的数据源,统一了对于数据的定义和采集方式,实现数据变更的及时反馈和实时共享,方便数据查询检索,图文档信息的完善和查阅,对于设计过程上下文环境结构部件的可视化参考,以及设计过程数据库调用提供了支持。
2.4建设基于“APQP” 的质量管理体系
通过数字化平台,结构化管理覆盖完整TS16949流程的所有数据,并保持数据的关联性,减少数据的重复录入,确保数据高效准确流转,涵盖从报价与项目确定(RFQ),产品设计与开发(CAD BOM/EBOM/DFEMA/DVP),过程设计与开发(MBOM/PFEMA/CONTROL PLAN/SOP),产品与过程验证(MSA/SPC/PPAP)到反馈评定和纠正措施(SPC/CI)。
2.5-建设基于“造型工程一体化” 的造型管理
基于模型的平台设计,从草图、效果图、CAS面、A面到造型工程一体化,材质渲染效果和AR/VR评审,皆可以通过平台实现。
2.6建设基于“设计导航” 的多专业协同设计
通过数字化平台的知识管理体系和知识工程模块应用,企业可以在开启新的项目设计中,实现知识重用。专业平台具有尺寸参数化、设计模板化、过程智能化特点,可以使设计过程自动检查设计规则,选择适当标准,自动设计客户化组件等,大大提升设计效率。
2.7建设基于“单一数据库” 的实时在线协同设计
对于异地研发设计和生产的企业,启用数字化平台,将极大提高工作效率和沟通效率。基于单一数据库,多地的工程师,主机厂,供应商等可以实现跨地域的在线协同,远程通过屏幕,共享信息,圈注和标记项目设计细节,通过聊天工具,完成在线的高效协作。
2.8建设基于“设计仿真一体化”
仿真体系 基于达索系统3DExperience平台的设计仿真一体化,设计变化后,分析模型自动更新,设计工程师直接使用分析模板进行快速分析,设计人员不需要专业的CAE知识背景,即可完成设计到仿真一步到位,从传统的开发窜行流程迭代为敏捷开发的并行流程。
通过达索系统3DExperience数字化平台实现应用场景的落地,来辅助企业进行研发制造,以应对变化的市场需求,将是企业必须长期修炼和提升的内功。选择具有强大背景的达索系统3DExperience平台,来协助企业打通自身和供应链的关系,极大提高整体的设计能力和制造能力,将是企业未来求生求变的主旋律。